Diagnóstico e Prevenção de Avarias em Equipamentos
9ª EdiçãoQuando um equipamento avaria, o caos instala-se e é exigida uma solicitação urgente da manutenção. Para isso é importante a manutenção estar bem preparada para identificar o problema e agir rapidamente no sentido de colocar o equipamento em funcionamento, que foi para isso que ele foi concebido.
Nesta formação propomos debater técnicas de identificação de problemas em automatismos e sistemas mecânicos, que ajudam a tomar decisões rápidas e corretas para que a solução seja definitiva e nunca provisória. Isto é, atuar na causa e não no efeito.
TOPONo fim do Curso, os Formandos serão capazes de:
- Interpretar a base de funcionamento de automatismos em logica cablada;
- Conhecer a base de funcionamento de automatismos em logica programada;
- Aplicar e regular as proteções adequadas de motores elétricos;
- Conhecer os diversos tipos de acionamentos de motores elétricos;
- Identificar e analisar diversos tipos de sensores e atuadores;
- Aplicar métodos de diagnósticos eficazes na resolução de avarias;
- Analisar casos práticos;
- Desenvolver sentido critico na análise dos equipamentos;
- Utilizar equipamentos de diagnóstico simples para detetar problemas precocemente;
- Compreender quais as tarefas que contribuem para uma Manutenção eficaz;
- Passar a ser proativo na deteção de avarias.
PARTE I – Automatismos Industriais (8 horas) – Eng. Bruno Carvalho
- Conceito de automatismo;
- Lógica Cablada e Logica Programada;
- Sistemas de acionamento de motores por contactores:
– Arranque simples de um motor;
– Inversão do sentido de rotação;
– Arranque estrela- triangulo. - Considerações gerais acerca da interpretação esquemática de circuitos com contactores;
- Proteções dos motores elétricos e regulação dos reles térmicos;
- Principais causas de avarias e diagnóstico em automatismos com base em contactos;
- Resolução de avarias;
- Tipos de acionamentos de motores elétricos:
– Variadores de velocidade;
– Soft starts;
– Vantagens e inconvenientes;
– Análise de problemas;
– Diagnóstico de avarias; - Automação com base nos PLCs:
– Ferramentas e equipamentos importantes para a resolução de problemas;
– Tipos de entradas e saídas;
– Modo de funcionamento de um PLC;
– Sensores e atuadores;
– Modo de funcionamento de diversos sensores e verificação técnica;
– Análise de problemas e possíveis soluções. - Organização geral do quadro elétrico e sua manutenção;
- Análise casos práticos. Resolução de avarias.
PARTE II – Sistemas Mecânicos (8 horas) – Eng. Pedro Rompante
- Execução de inspeções visuais;
- Equipamentos mecânicos:
– Rolamentos:
– Características Funcionais;
– Métodos de montagem;
– Requisitos de Manutenção.
– Correias:
– Identificação de avarias.
– Rodas dentadas:
– Tipos construtivos;
– Deteção de problemas;
– Causas típicas de avarias.
– Fissuras e alterações dimensionais:
– Avaliar tipo de fratura e a razão de ter ocorrido;
– Compreender o processo de perda de material.
– Vibrações mecânicas:
– Origem das vibrações;
– Formas construtivas de minimizar as vibrações.
– Pneumática:
– Componentes essenciais de uma rede de ar comprimido;
– Análise e interpretação dos esquemas técnicos;
– Deteção de fugas de ar comprimido.
– Óleo-Hidráulica:
– Componentes essenciais de um sistema óleo-hidráulico;
– Análise e interpretação dos esquemas técnicos;
– Minimizar contaminação;
– Requisitos de filtragem.
– Lubrificação com massa:
– Entender as características das massas;
– Determinar a quantidade ideal de massa a aplicar;
– Boas práticas.
– Corrosão:
– Tipos de Corrosão e origens habituais;
– Como evitar Corrosão.
– Equipamentos de Medição:
– Como selecionar;
– Como utilizar;
– Quando verificar, calibrar e aferir. - Utilização de equipamentos de diagnóstico:
– Termómetro;
– Câmara Termográfica;
– Paquímetro;
– Estetoscópio;
– Ultrassons. - Condições de armazenamento de peças mecânicas para evitar danos;
- Análise funcional de um equipamento:
– Zonas perigosas;
– Análise do manual do fabricante;
– Analisar a relação entre sistemas;
– Determinar as necessidades de manutenção essenciais;
– Compreender requisitos legais a aplicar. - Limpeza técnica.
- Operadores de máquinas;
- Técnicos de Manutenção Industrial;
- Gestores e chefes de equipa de Manutenção;
- Chefes de equipas de Produção;
- Operadores de Produção;
- Eletricistas;
- Instaladores;
- Eletromecânicos;
- Responsáveis de Manutenção Industrial;
- Quadros técnicos;
- Outros Profissionais de engenharia eletrotécnica e não eletrotécnica;
- Todos aqueles que se interessem pelo tema.
- Método expositivo, ativo e interativo com recurso a multimédia;
- Utilização de equipamentos de teste nos equipamentos;
- Literatura de Apoio com exemplos de casos práticos.
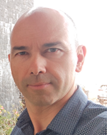
Bruno Carvalho
Licenciatura em Engenharia Automação e Controlo – Universidade Moderna Porto (pré-Bolonha). Desde 2005 na área eletrotécnica como gestor de produto nas áreas, média tensão, automação, compensação da reativa e carregadores de VE´s, na empresa “Bifase, Lda.” Em 2023 integrou a equipa de engenharia da empresa CIRCUITOS – Energy Solutions, Lda. Formador profissional em diversas entidades. Especialista nas áreas de compensação de energia reativa baixa e média tensão, corte e proteção, quadros elétricos, variação de velocidade e carregadores de veículos elétricos. Auditor e perito de instalações elétricas em média e baixa tensão. Credenciado pela ADENE enquanto Auditor Interno em Sistemas de Gestão de Energia com base no referencial ISO 50001. Membro da Ordem dos Engenheiros como membro efetivo do colégio de Engenharia Eletrotécnica. Técnico responsável de várias instalações elétricas de serviço particular em média tensão.
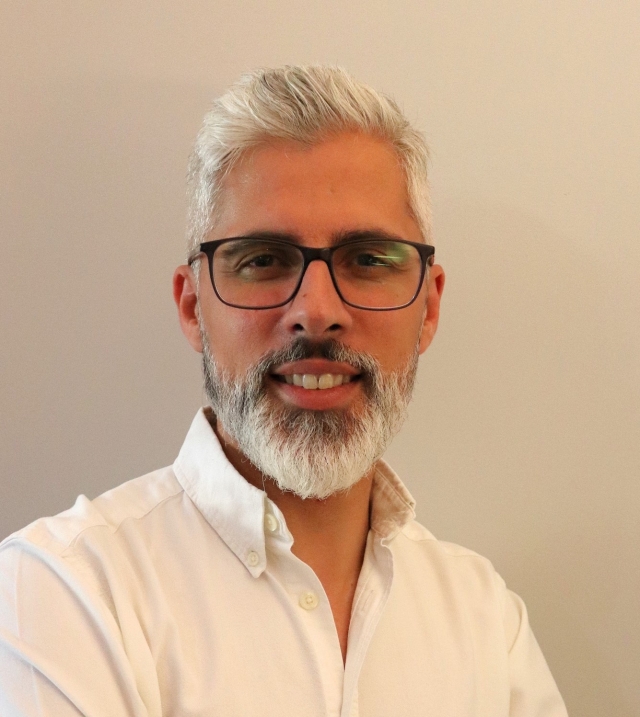
Pedro Rompante
Especialista em Manutenção Industrial pela OE (Ordem dos Engenheiros). Engenheiro Mecânico (Faculdade de Engenharia da Universidade do Porto). Membro sénior da OE (Ordem dos Engenheiros). Membro da ATEHP (Associação dos Técnicos de Engenharia Hospitalar Portugueses). Membro da APMI (Associação Portuguesa de Manutenção Industrial). Formador certificado pelo IEFP. Formador nos temas da Manutenção Industrial, com mais de 450 horas de formação efectuadas, para mais de 480 formandos. Membro de Júri para as Provas de Mestrado, em várias instituições do Ensino Superior Desde 2014 é Coordenador Técnico da Especialização em Manutenção Industrial do CENERTEC. Desde 2019, é Diretor de Engenharia e Gestão Industrial no CENERTEC. Consultor Independente de Manutenção. Orador em Encontros e Congressos Nacionais e Internacionais. Contributos regulares para revistas da Especialidade, como a revista “Manutenção”, da APMI. Experiência de Manutenção e Gestão de Operações nas seguintes áreas: Gestão de frotas automóveis; Gestão e tratamento de resíduos; Equipamentos de Movimentação de Terras e Construção de Estradas; Centrais térmicas; Sistemas de Tratamento de Águas; Sistemas Automáticos de Lavagem; Equipamentos Sob Pressão; Equipamentos Médicos de Medição e Fiação Têxtil. Principais tarefas no âmbito da Manutenção Industrial: – Organização e Gestão da Manutenção, em contexto fabril; – Análise, planeamento estratégico e operacional das operações de Manutenção preventiva, corretiva e condicionada; – Definição e implementação de Sistema de Informação para controlo da Manutenção; – Liderança do projeto de recodificação dos artigos do armazém da Manutenção; – Implementação da metodologia RCM para elaboração de planos de manutenção; – Responsável pela análise de avarias e implementação de medidas para prevenir a sua recorrência; – Afetação, coordenação e utilização de equipamentos no âmbito da Produção; – Definição e implementação de planos de controlo de condição de equipamentos, em âmbito industrial, incluindo o return-on-investment. Principais tarefas no âmbito da Gestão de Operações: – Seleção, formação e orientação de equipas de operadores; – Organização e afetação de recursos para a execução das tarefas produtivas; – Análise, planeamento estratégico industrial, definição de planos de ação para investimento; – Licenciamento da atividade industrial, incluído Licenciamento Ambiental; – Licenciamento de equipamentos sob pressão e componentes associados; – Elemento de ligação às entidades oficiais, respondendo a dúvidas e prestando esclarecimentos.
ONLINE / LIVE
Como Funciona esta Formação Online/Live em Direto?
- Fazer inscrição nesta página
- Após a inscrição e pagamento, os Participantes irão receber um link de acesso para clicarem e entrarem na plataforma à hora marcada.
- A formação será dada em formato Online/Live, à hora marcada, em Direto.
- Esta plataforma é muito simples de utilizar e permite que haja interactividade. Os participantes poderão participar, comentar, fazer perguntas, tirar dúvidas, por escrito ou por voz, em tempo real.
Esta formação, com a duração de 16 horas, funcionará nos seguintes dias:
7, 9, 15 e 16 de Julho de 2025
09:00 – 13:00
O valor da inscrição é de 390.00 € + IVA (23%), valor total de 479,70 € pagável ao CENERTEC até à data de realização do Curso e inclui:
- Acesso à Plataforma E-Learning
- Acesso à Documentação de Apoio
- Certificado SIGO
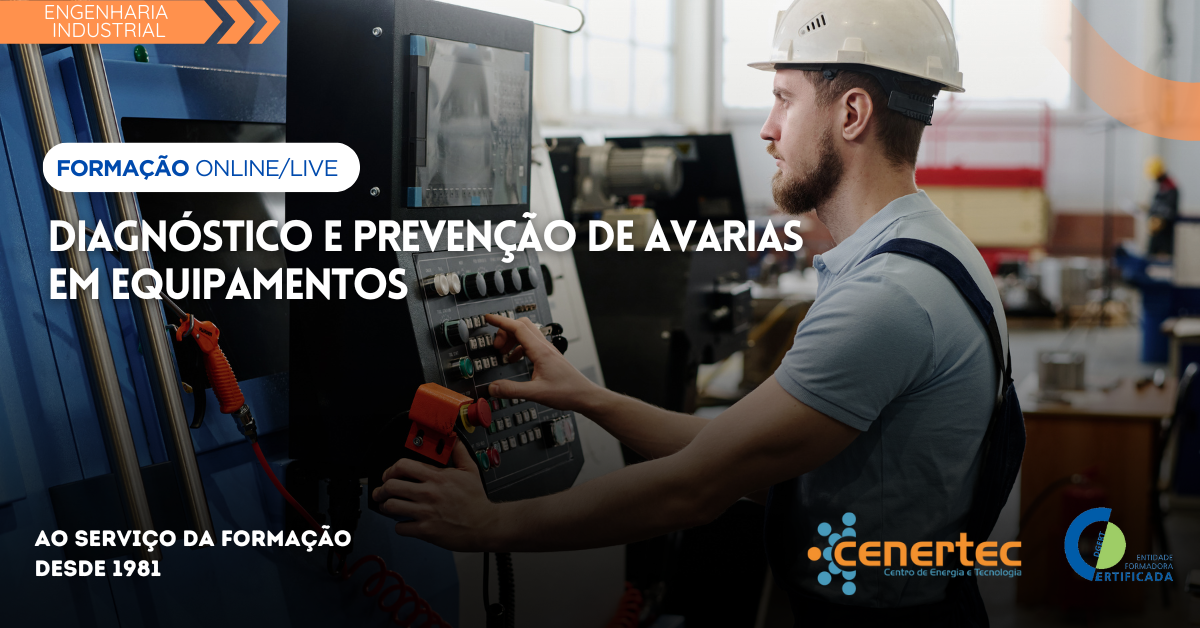